El inventario como consecuencia - Mejorar la planificación de los suministros
Introducción
Gestionar la eterna lucha entre el exceso de inventario y la falta del mismo es la clave de una gestión eficaz de la cadena de suministro, pero es una ecuación que las organizaciones no consiguen resolver continuamente.
Es una situación típica: a la empresa no le gusta la cantidad de existencias que tiene, así que se da la orden de reducirlas. La producción se detiene hasta que el inventario se reduce a un nivel aceptable, sólo para descubrir, unas semanas más tarde, que los clientes están descontentos porque no pueden conseguir los productos que quieren. Así que la producción se reinicia y funciona a toda máquina durante los meses siguientes para intentar recuperar la posición de suministro. ¿Cuál es el resultado? La empresa acaba teniendo más existencias de las que tenía al principio.
Sin embargo, cuando se trata de optimizar el inventario, las opciones van mucho más allá de simplemente detener la producción. La respuesta es una planificación eficaz del suministro. Analizando adecuadamente las decisiones que toma en relación con los niveles de servicio, los tiempos de ciclo, la utilización de la capacidad de producción y las existencias de seguridad, una organización puede crear una lista de opciones para asegurarse de que siempre tiene la cantidad adecuada.
En lugar de esperar a que el próximo valiente se limite a detener la producción hasta agotar las existencias y dejar que la historia se repita, es necesario un cambio de paradigma.
Nivel óptimo de existencias
Sólo cuando una organización puede definir qué inventario necesita para gestionar eficazmente su negocio y alcanzar sus objetivos, puede controlar al "monstruo del inventario" y realizar mejoras duraderas. Pero, ¿cómo decide una organización cuál es el nivel "adecuado"?
Existen muchas fórmulas para calcular el stock de seguridad de una empresa en función de: la variación de la oferta y la demanda, los plazos de entrega y el nivel de servicio que la empresa se propone obtener. Pero eso es lo fácil, y antes de empezar por este camino la empresa debe dar un paso atrás y revisar las razones por las que tiene existencias en primer lugar.
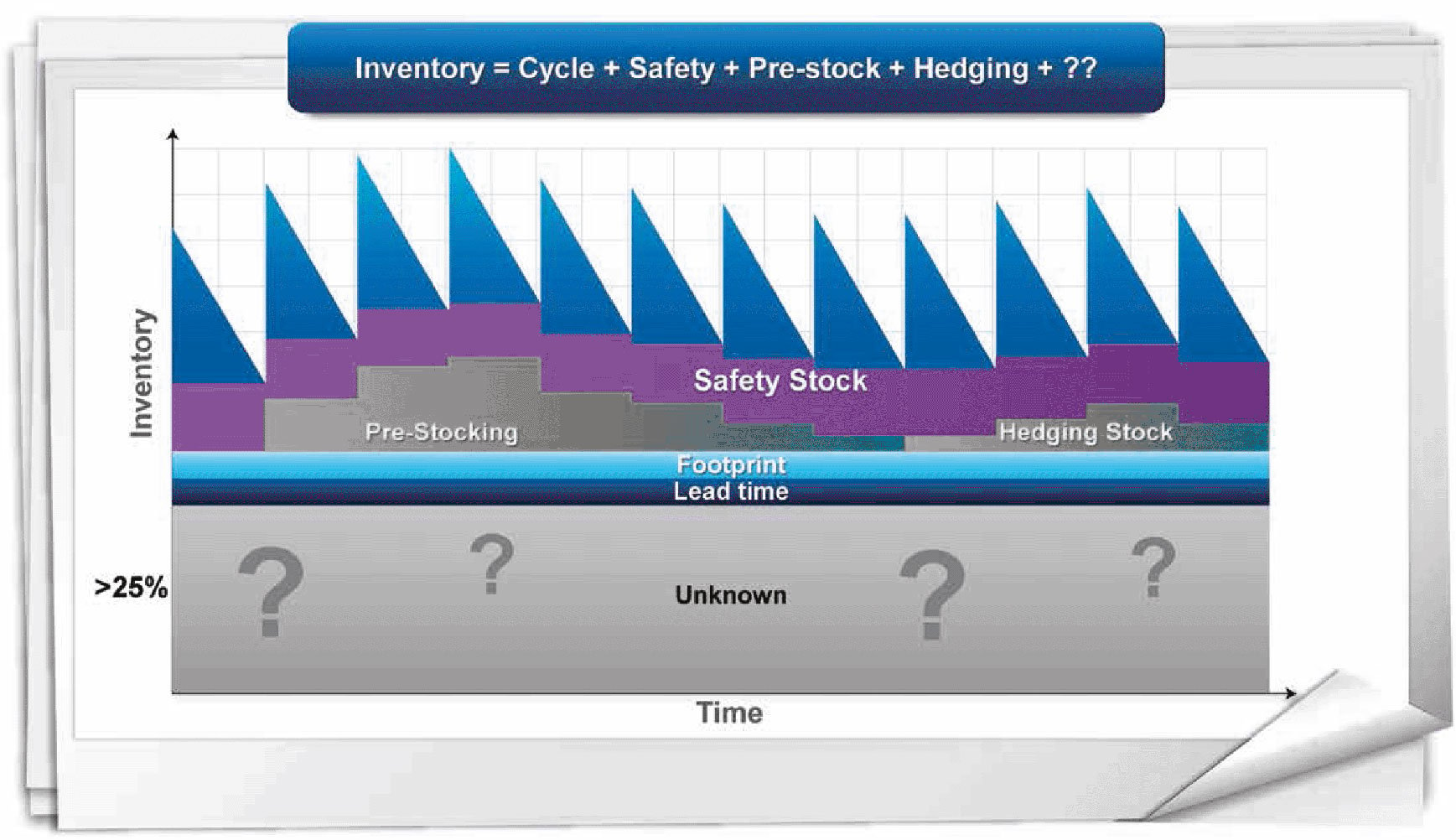
Con demasiada frecuencia, las empresas se apresuran a eliminar las existencias visibles (existencias cíclicas, de seguridad, de preabastecimiento y de cobertura). Sin embargo, como muestra la figura 1, es en el resto, lo que no se ve, que puede suponer hasta el 25% del inventario de una empresa, donde deben concentrarse los esfuerzos.
Sin embargo, no basta con eliminar de un plumazo el inventario desconocido. Intentar eliminar el inventario sin abordar la causa raíz es como abordar los síntomas de una enfermedad antes del diagnóstico. Es fundamental entender primero por qué está ahí y después poner en marcha un plan de acción bien meditado para eliminarlo.
Inventario como consecuencia
¿Cómo se crea el inventario? Es el resultado de muchas cosas que una empresa hace o deja hacer inconscientemente y que pueden clasificarse en tres categorías (como se muestra en la figura 2): variación y error, ineficacia y toma de decisiones estratégicas y tácticas. Una organización tiene que controlar cada uno de estos aspectos antes de poder gestionar su inventario con eficacia y, a su vez, ser ágil y eficiente.
Una causa obvia del inventario es la variación que se produce entre la oferta y la demanda; en un mundo hipotético en el que las organizaciones tuvieran un 100% de precisión en las previsiones, no habría necesidad de existencias de seguridad. En la realidad, por supuesto, las organizaciones suelen estar plagadas de previsiones de demanda inexactas y demasiado celosas y, como consecuencia, acaban teniendo demasiadas existencias. También los errores -ya sea comprar materiales equivocados, fabricar productos fuera de especificación o de mala calidad, o utilizar datos erróneos en la previsión y la planificación- generan existencias innecesarias.
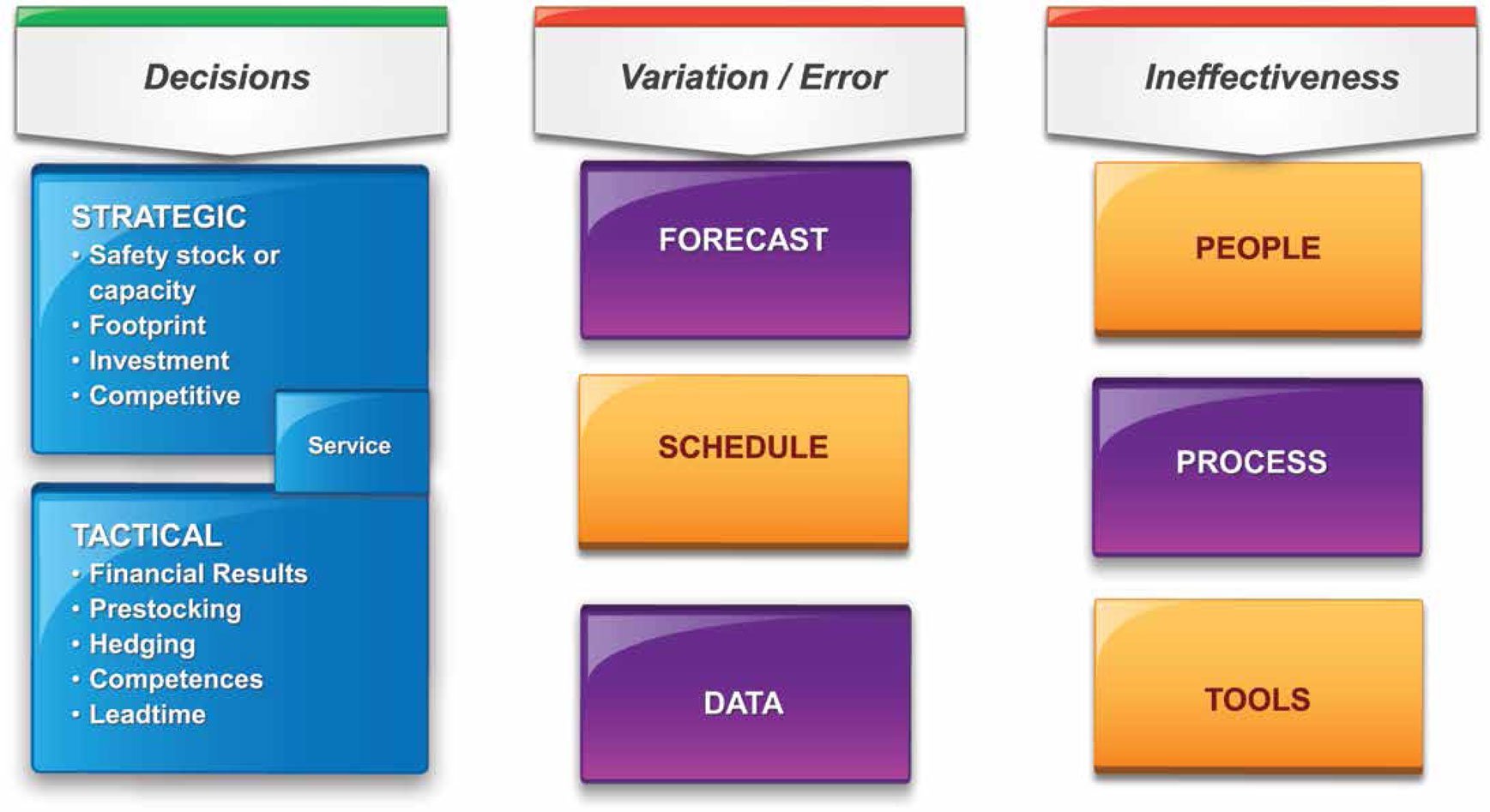
Menos obvio es el inventario creado como consecuencia de la ineficacia de las personas, los procesos y las herramientas. Un ejemplo común: las empresas que no tienen un sistema ERP (sí, todavía hay muchas) y realizan cálculos de tipo MRP en una hoja de cálculo, a menudo sólo lo hacen semanal o mensualmente debido al tiempo que lleva. En consecuencia, estas empresas suelen mantener un stock de seguridad más elevado "por si acaso".
Pero lo más importante es que el inventario es consecuencia de las decisiones estratégicas y tácticas que toma una empresa; las decisiones sobre el número de puntos de suministro en la cadena de suministro, los niveles de servicio requeridos o el nivel de eficiencia de fabricación necesario tienen un enorme impacto en el inventario. Sorprendentemente, el inventario que una organización tiene hoy en día suele ser consecuencia de las decisiones que tomó hace meses, años o incluso décadas. Cuando toman estas decisiones, las empresas no reconocen el impacto a largo plazo que tienen en el inventario y, en su lugar, fijan objetivos arbitrarios sobre la base de un determinado número de semanas de cobertura. De este modo, los responsables de las decisiones cotidianas sobre el inventario no comprenden ni controlan las palancas que afectan a los objetivos de inventario, y la pobre alma a la que se da el título de "Responsable de Inventario" a menudo no es más que una niñera del inventario, sin poder real para influir en su existencia.
No elimine el inventario; cambie la forma de gestionarlo
Una vez comprendida la causa del inventario, es hora de abordar cómo gestionarlo. La Planificación Empresarial Integrada (S&OP avanzada) puede proporcionar el control sobre los procesos, la visibilidad para planificar y una toma de decisiones eficaz, que son fundamentales para acertar con el inventario.
La Planificación Empresarial Integrada (PEI) se sitúa en el corazón de muchas organizaciones como el proceso de gestión que dirige el negocio, alineando los planes estratégicos y tácticos cada mes y asignando los recursos críticos -personas, equipos, inventario, materiales, tiempo y dinero- para satisfacer a los clientes de la forma más rentable.
A medida que una empresa desarrolla su proceso de PNI, alcanzará diferentes fases de madurez, pasando de los procesos de gestión incombustibles e inconexos de la fase 1 al control de los procesos empresariales de la fase 2. La figura 3 muestra las mejoras que debe introducir una empresa para atajar la causa principal del inventario a lo largo de este proceso de madurez.
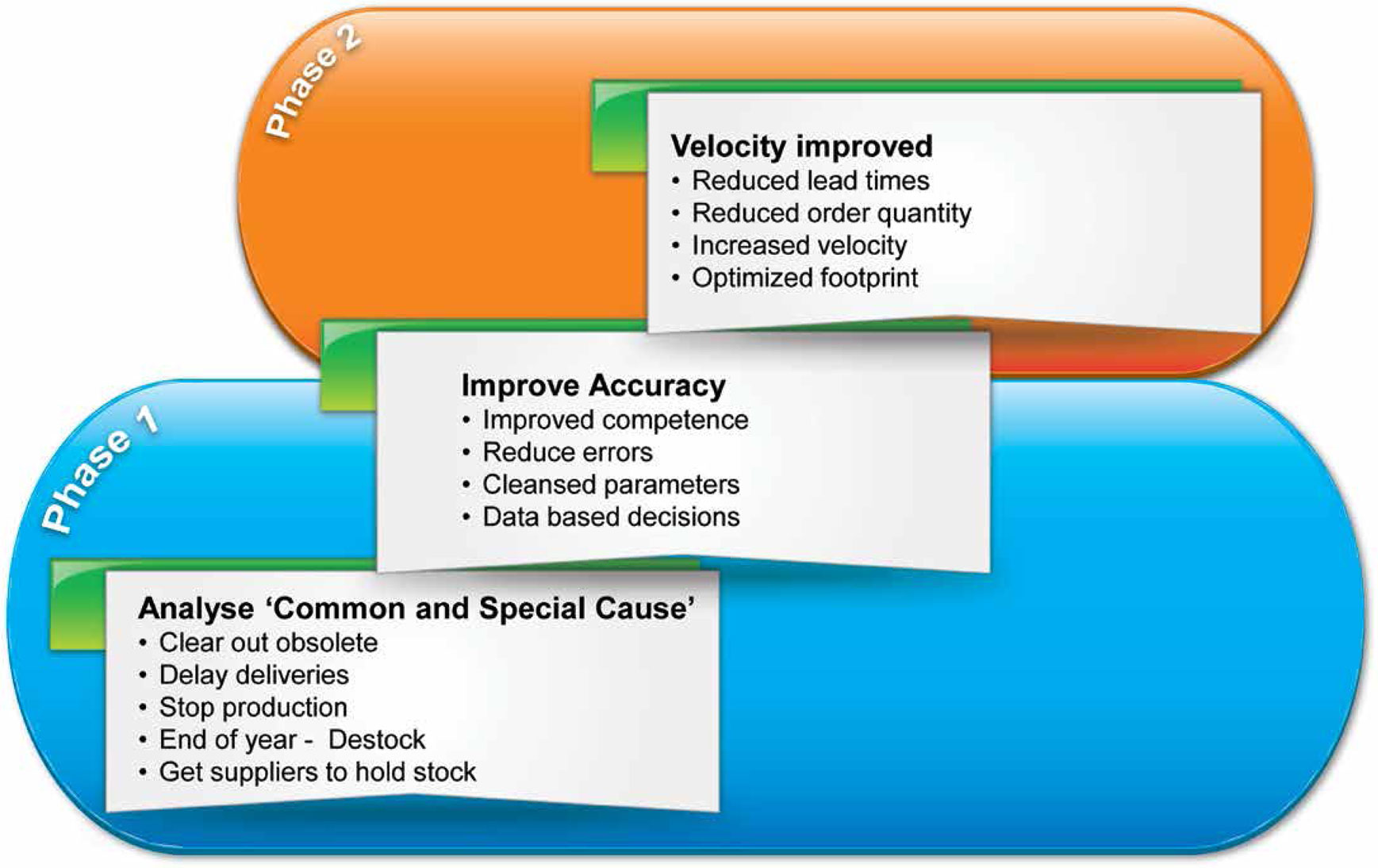
En la fase 1 hay que combatir la ineficacia y la imprecisión. Aquí, las organizaciones tienen que eliminar la variación como prioridad, eliminando los grandes errores de proceso. Deben conocer bien sus procesos empresariales y asegurarse de que se ejecutan de forma coherente. Para que una empresa llegue a la cima de la fase 1, debe tener "el control" y hacer todo lo que planea hacer, según lo previsto, al menos el 95% de las veces. Con la mejora de la comprensión y la planificación que una organización obtiene en la fase 1, es posible eliminar gran parte del inventario desconocido que posee.
Al pasar de la fase 1 a la 2, las organizaciones empezarán a comprender el impacto de las decisiones y a tener en cuenta el inventario en las decisiones que tomen. El IBP proporciona al equipo directivo una visión clara de los problemas y las diferencias entre los resultados previstos, establecidos en los planes estratégicos/de negocio descendentes, y la proyección ascendente de hacia dónde se dirige realmente la empresa. El IBP hace especial hincapié en la gestión de hipótesis y la planificación de escenarios, para garantizar que los responsables de la toma de decisiones tengan en cuenta todas las alternativas posibles y puedan elegir con confianza la que consideran la mejor.
Gestión de existencias
Como ya se ha comentado, cuando se trata de tomar decisiones relativas al inventario, detener la producción rara vez es la respuesta y las organizaciones deben tener en cuenta todas las variables de suministro para gestionar su inventario de forma eficaz, mirando más allá de la ventana de ejecución inmediata antes de tomar decisiones críticas.
Nivel de servicio frente a existencias de seguridad
En cuanto una empresa supera un nivel de servicio del 95%, la cantidad de existencias de seguridad que necesita para prestar ese servicio aumenta considerablemente. La figura 4 muestra el factor multiplicador que se aplica en el cálculo de las existencias de seguridad, en función del nivel de servicio. Cuando una organización fija su objetivo de nivel de servicio, debe considerar detenidamente el impacto que esto tiene en el inventario; aumentar los niveles de servicio implica tener más existencias de seguridad para no defraudar al cliente.
Las empresas deben plantearse dos preguntas:
- ¿Realmente tenemos que dar un nivel de servicio del 100%?
- ¿Reconocemos lo que cuesta ofrecer un nivel de servicio del 100% y el estrés que ello supone para las personas?
En un mundo ideal, todas las organizaciones tendrían niveles de servicio del 100%; la realidad es que muchas tienen que conformarse con el 95%. La evaluación comparativa de la organización y el estudio de la oferta de la competencia son requisitos esenciales para determinar un nivel de servicio aceptable. Fíjese también en lo que espera el mercado.
Por ejemplo, el 95% puede ser suficiente para la mayoría de las industrias, pero para las industrias farmacéutica y médica el 95% no es suficiente. En el pasado, las cadenas de suministro farmacéuticas optaban por altos niveles de servicio en lugar de agilidad en la fabricación, manteniendo altos niveles de inventario y costes de transporte para evitar la falta de existencias. Pero el auge de los genéricos frente a los productos patentados, unido al elevado coste de desarrollo de los medicamentos, ha ejercido una enorme presión sobre la cadena de suministro. Como resultado, ya no es aceptable que las cadenas de suministro farmacéuticas tengan un exceso de existencias. Pero cuando la vida puede depender literalmente del suministro de productos, las farmacéuticas deben seguir aspirando a unos niveles de servicio del 98%, construyendo las cadenas de suministro en torno a una planificación de la demanda muy precisa.
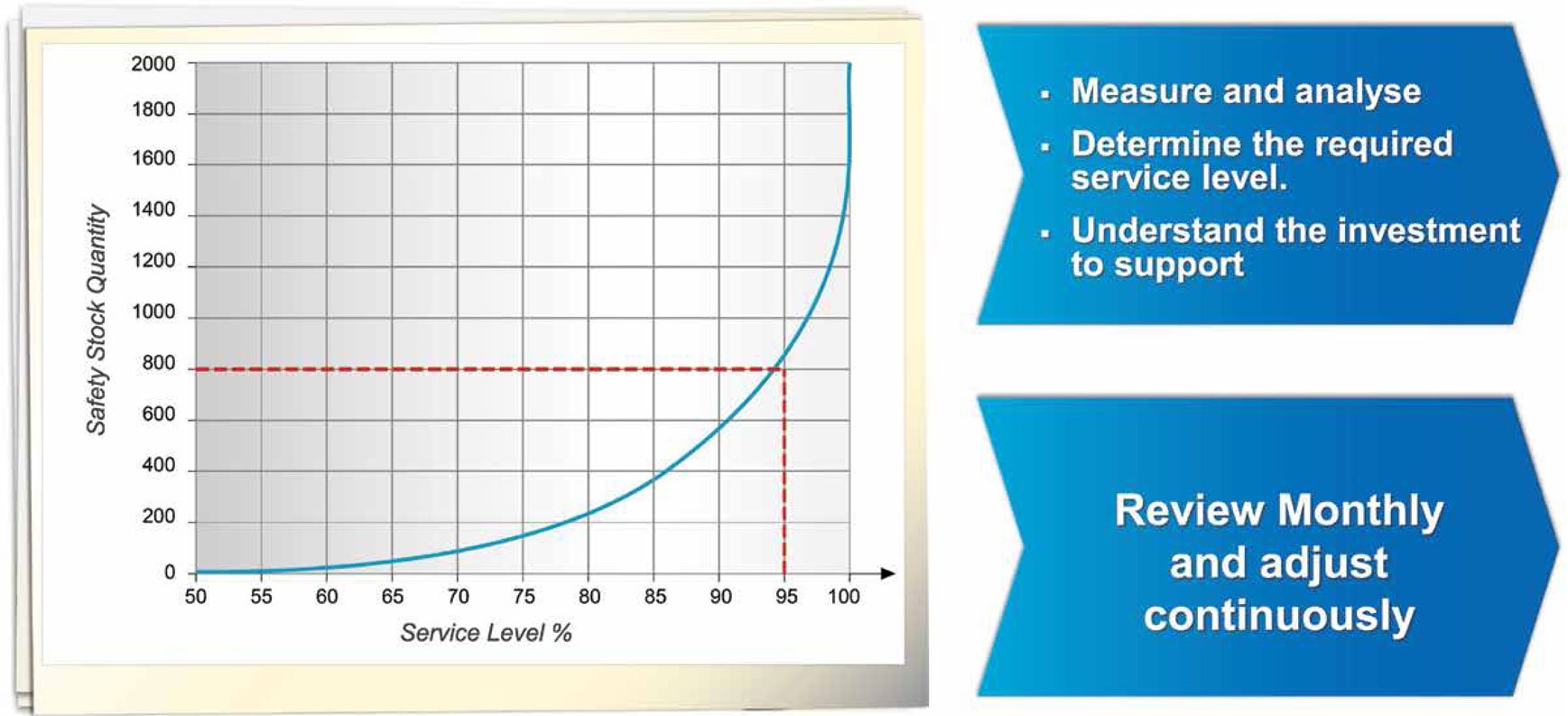
Este tipo de análisis de mercado debe hacerse empresa por empresa para descifrar qué niveles de servicio puede permitirse la organización.
Una organización con la que trabajó Oliver Wight se enfrentaba a la tarea de reducir el inventario en un 25%. Para este fabricante mundial de productos químicos, el incumplimiento de su objetivo tenía graves consecuencias financieras. Estaba claro que reducir la producción sin cambiar los parámetros no iba a hacer otra cosa que causar problemas de suministro. La empresa operaba con niveles de servicio del 98% para lograr una ventaja competitiva, pero si bajaba al 95% era posible reducir sustancialmente el inventario. La consecuencia era un ligero aumento del riesgo de que algunos clientes no recibieran el producto a tiempo, pero el ahorro potencial lo compensaba con creces. ¿El resultado? Una reducción de las existencias de seguridad por valor de medio millón de dólares.
Reducción del tiempo de ciclo
Otra división de la misma empresa se enfrentó a un reto similar de reducción de existencias. Pero en este caso la solución era diferente: la división realizaba largas campañas en aras de la eficiencia operativa, pero al fabricar la mitad, con el doble de frecuencia, conseguía una reducción sustancial de las existencias de ciclo. El riesgo era tener que hacer cambios más frecuentes, pero a la larga la respuesta al mercado sería más ágil. Y con tiempos de ciclo más cortos, había menos posibilidades de obsolescencia. El stock de ciclo se redujo en 500 toneladas, con una reducción adicional de 150 toneladas en el stock de seguridad; un impresionante 40% del inventario total de ese grupo de productos.
Gestión de la capacidad de seguridad
La mayoría de las organizaciones consideran que el inventario es su única opción para amortiguar los malos resultados del suministro y proporcionarles la flexibilidad necesaria para satisfacer una demanda imprevista. Pero, de hecho, invertir en capacidad de seguridad, como parte de la estrategia de suministro, puede ser una opción más barata. En lugar de considerar que el objetivo de la organización es maximizar la utilización de los activos y poner la planta al 100% de su capacidad, reducir su uso al 90% y tener la capacidad de aumentarla cuando la demanda lo requiera puede reducir la cantidad de existencias necesarias. La fabricación flexible reduce, en última instancia, la inversión, los costes corrientes y los riesgos asociados al exceso de existencias.
Gestión de las existencias de seguridad
Normalmente, por falta de comprensión de la verdadera variación de la oferta y la demanda, muchas empresas tienen un stock genérico de seguridad de dos semanas para cada producto de su cartera. Pero es importante tener en cuenta la importancia de cada producto. Los que son más estratégicos o tienen requisitos más estrictos (e incluso contractuales) de los clientes, pueden requerir un mayor nivel de servicio y, por tanto, mayores existencias. Piense también en los productos cuya demanda varía tan poco que apenas se necesitan existencias de seguridad, ya que las necesidades pueden predecirse con gran exactitud. Si las existencias de seguridad no se utilizan nunca, ¿para qué tenerlas? La regla sencilla es poner existencias donde ayuden al negocio y reducirlas donde sobren.
Un cambio cultural
Al cambiar la forma de gestionar el inventario, habrá que superar problemas de comportamiento y silos funcionales. A menudo es la fabricación la que dicta cuánto se fabrica, en lugar de basar la producción en las necesidades de la empresa. Del mismo modo, la demanda suele imponer previsiones elevadas para garantizar que los clientes reciban sus pedidos a tiempo.
Cuidado con este sesgo en los negocios; mata las cadenas de suministro y puede acabar con las empresas. Afortunadamente, es evitable. Si la demanda y el suministro se responsabilizan conjuntamente del inventario, las organizaciones pueden mejorar la precisión de las previsiones. Esta propiedad conjunta, sin embargo, implica un cambio cultural: derribar las barreras departamentales, eliminar la cultura de la culpa y crear un entorno basado en el trabajo en equipo, en el que todos estén alineados con la estrategia.
La Planificación Empresarial Integrada ayuda a abordar estos paradigmas porque derriba las barreras organizativas tradicionales y crea una estructura basada en procesos integrados.
El reto consiste en aplicar un programa de gestión del cambio en paralelo a la Planificación Empresarial Integrada, de modo que se modifiquen los comportamientos y puedan aprovecharse todas las ventajas de los procesos y equipos integrados. Las personas deben tener claro cuáles son sus funciones y responsabilidades. Y cuando se trata de inventarios, hay muchas personas implicadas; entre las personas que ejercen una influencia decisiva se encuentran las que afectan a las finanzas, el riesgo, el servicio, el plazo de entrega, la huella, las existencias cíclicas, la frecuencia de planificación y las existencias de seguridad. Identificar a estos actores clave y dotarles de los conocimientos necesarios les permite aplicar las mejores prácticas dentro de sus funciones y responsabilidades claramente definidas. Las personas son el arma más poderosa de la organización para gestionar eficazmente el inventario y crear una empresa ágil y eficiente.
Conclusión
El inventario no es algo que deba abordarse simplemente cuando surge un problema grave. A medida que las cadenas de suministro se hacen más largas y complejas y persiste la volatilidad económica mundial, controlar el inventario es esencial para satisfacer de forma rentable las demandas del consumidor actual.
Con un proceso de Planificación Empresarial Integrada en marcha, una empresa estará equipada con el control, la visibilidad y el apoyo para una toma de decisiones eficaz que necesita para gestionar el inventario.
Si se tienen en cuenta todas las variables de suministro: niveles de servicio, duración de los ciclos, utilización de la capacidad de producción y existencias de seguridad, se obtendrá una lista de opciones razonables para gestionar el inventario. Así, en lugar de limitarse a detener la producción, la organización puede tomar decisiones con conocimiento de causa, predecir con mayor exactitud el inventario total en la planificación a largo plazo y fijarse continuamente objetivos de reducción.
En última instancia, cambiar la forma de gestionar el inventario ayudará a crear una empresa ágil y eficiente.