El éxito de la cadena de suministro de Santa Claus avergüenza los planes de construcción de viviendas del gobierno británico
23 de diciembre de 2024
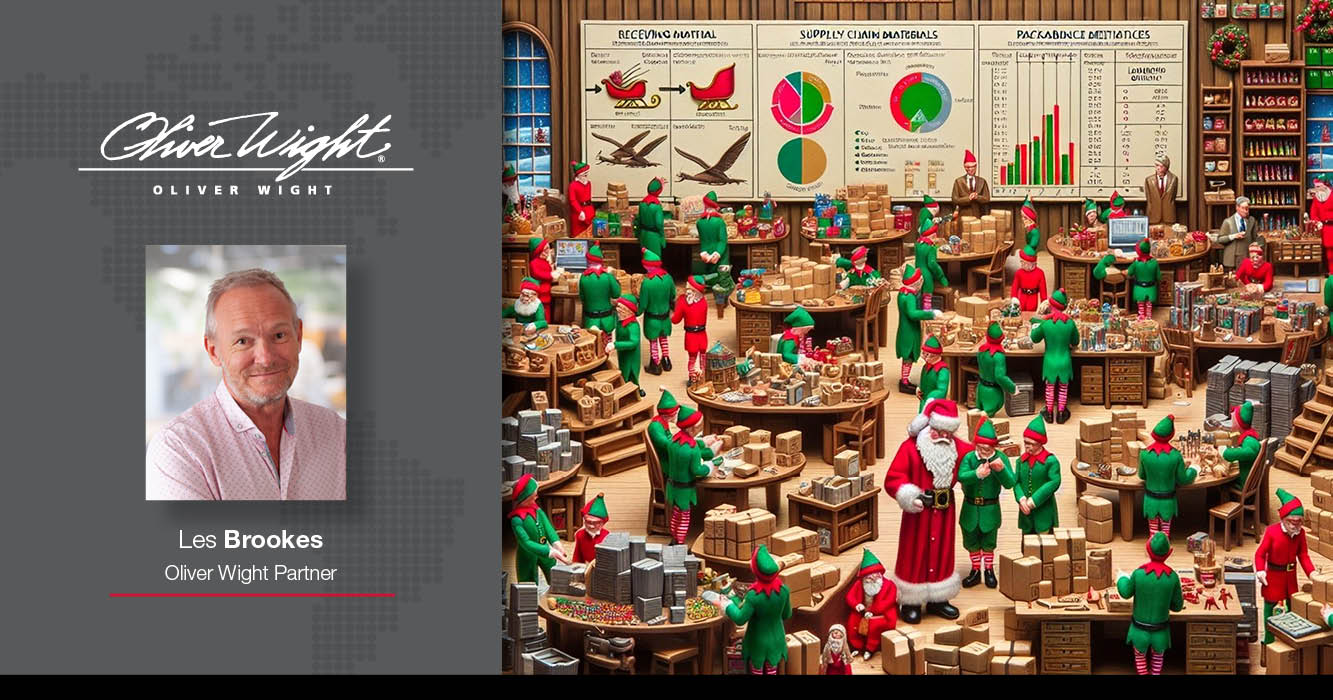
Mientras los niños de la lista de los "buenos" esperan ansiosos sus regalos de Navidad, podemos estar razonablemente seguros de que Papá Noel y sus duendes han hecho sus deberes de planificación de la cadena de suministro. Ojalá pudiera decirse lo mismo de los ambiciosos objetivos británicos en materia de construcción de viviendas.
La promesa electoral laborista de construir 1,5 millones de viviendas para 2029 -repetida por el primer ministro Sir Keir Starmer a mediados de diciembre- es un duro recordatorio de lo crítico que es el análisis de principio a fin a la hora de establecer objetivos de crecimiento de gran alcance.
La ambición de atajar la crisis de la vivienda en Gran Bretaña es a la vez necesaria y encomiable: pocos estarían en contra de la necesidad urgente de más viviendas asequibles, en particular para las generaciones más jóvenes. El objetivo refleja una auténtica comprensión de la importancia social y económica de la accesibilidad de la vivienda.
Sin embargo, mientras que el taller de Papá Noel puede haber perfeccionado su planificación de la producción a lo largo de los siglos, la industria británica de la construcción se enfrenta a un reto mucho más complejo que parece haber sido dramáticamente subestimado por el gobierno.
Aprender de los errores del pasado
La historia ofrece lecciones aleccionadoras sobre grandes promesas que flaquearon en su ejecución. Las predicciones recientes sobre la adopción de los vehículos eléctricos pasaron por alto las limitaciones críticas de los materiales de las baterías. Numerosos proyectos gubernamentales de TI se derrumbaron bajo plazos poco realistas que ignoraban la complejidad de la integración de sistemas. La promesa de la vivienda sigue este patrón familiar: un objetivo que acapara titulares desconectado de la realidad operativa.
Como especialista en gestión y cadena de suministrome pregunto: ¿Cómo puede fijarse un objetivo tan amplio sin realizar antes un análisis exhaustivo de las limitaciones críticas?
Aunque la crisis de la vivienda exige con razón una acción audaz y unos objetivos ambiciosos, anunciar plazos sin comprender las limitaciones fundamentales corre el riesgo de socavar una iniciativa por lo demás meritoria. Luego, redoblar la ambición, a pesar de las advertencias de la Federación de Constructores de Viviendas (HBF) de que se necesitan decenas de miles de nuevos reclutas, agrava el reto de cumplir este importante objetivo.
Desglosar la realidad de la cadena de suministro
La complejidad comienza con las materias primas -yeso para placas de yeso, cemento, ladrillos y madera-, todas las cuales requieren importantes inversiones para aumentar su capacidad. Los grandes fabricantes, los verdaderos "gorilas" de la cadena de suministro de la construcción, toman decisiones cuidadosamente calculadas sobre la inversión en capacidad. Es poco probable que mantengan capacidad redundante, y las nuevas instalaciones de producción exigen enormes inversiones de capital y largos plazos de entrega.
La preparación del terreno plantea otro cuello de botella. La limpieza del terreno y la instalación de los servicios no sólo requieren operarios, sino topógrafos, arquitectos y especialistas diversos. Esto no se soluciona simplemente comprando más excavadoras: el capital humano cualificado tarda años en desarrollarse.
Tal vez lo más crítico sea la escasez de mano de obra cualificada. Las escuelas técnicas superiores que antaño formaban a electricistas, fontaneros, albañiles y pintores han cambiado su enfoque hacia la formación relacionada con la tecnología y los servicios. Incluso con una inversión renovada, nos enfrentamos a un plazo de dos a tres años antes de que los nuevos aprendices puedan contribuir de forma significativa. Las necesidades actuales de la industria son asombrosas: 20.000 nuevos albañiles, 20.000 trabajadores del suelo y 8.000 carpinteros, según los cálculos de la HBF.
Más ancho implicaciones para planificación empresarial
Lo que surge es un patrón familiar en todas las industrias: objetivos fijados sin comprender las implicaciones y limitaciones estratégicas en toda la cadena de valor. El éxito en la entrega requiere orquestar múltiples factores: materiales, capacidad de fabricación, mano de obra cualificada, logística y dinámica del mercado.
Aunque la mano de obra extranjera podría parecer una solución obvia, esto entra en conflicto con las actuales políticas de inmigración. El panorama posterior al Brexit ya ha mermado la mano de obra de la construcción de trabajadores europeos cualificados, lo que pone de relieve cómo las limitaciones políticas pueden ir en contra de los objetivos declarados.
Mientras tanto, el enfoque del gobierno en acelerar las aprobaciones de planificación, aunque importante, aborda el menor de los retos. Unas aprobaciones más rápidas sin resolver las limitaciones fundamentales de la cadena de suministro sólo ampliarán los bancos de suelo, fomentando potencialmente la especulación en lugar de la construcción - un caso clásico de tratar los síntomas en lugar de las causas.
Trazar un camino realista
El éxito requiere convocar a todas las partes interesadas -constructores de viviendas, proveedores de materiales, instituciones de formación y organismos profesionales- para desarrollar una verdadera comprensión de las limitaciones y capacidades. Sólo entonces podremos crear un plan viable que trace el ritmo necesario de mejora.
Este enfoque exige resistirse al encanto de los anuncios arrolladores en favor de una planificación detallada y práctica. En lugar de centrarse únicamente en el objetivo de 1,5 millones de viviendas para 2029, ¿por qué no complementar esta ambición con un análisis exhaustivo de las capacidades actuales, identificar las limitaciones críticas y desarrollar un enfoque por etapas que reconozca el tiempo necesario para crear capacidad? Esto aumentaría realmente la probabilidad de alcanzar este objetivo social vital.
A medida que nos acercamos a 2025, los líderes empresariales harían bien en aprender de este ejemplo. Tanto si se trata de construir casas como de fabricar productos, el crecimiento sostenible requiere algo más que objetivos audaces: exige un conocimiento profundo de las capacidades y limitaciones de principio a fin.
Mientras que Papá Noel puede haber perfeccionado su cadena de suministro a lo largo de siglos de práctica, el resto de nosotros necesitamos invertir tiempo en un análisis y una planificación adecuados. Después de todo, incluso el legendario y barbudo repartidor de regalos sabe que entregar con éxito millones de regalos en una noche requiere algo más que magia: exige años de cuidadosa preparación, creación de capacidad y establecimiento de objetivos realistas. Quizá sea hora de que nuestro gobierno reciba una clase magistral del experto en la cadena de suministro del Polo Norte.